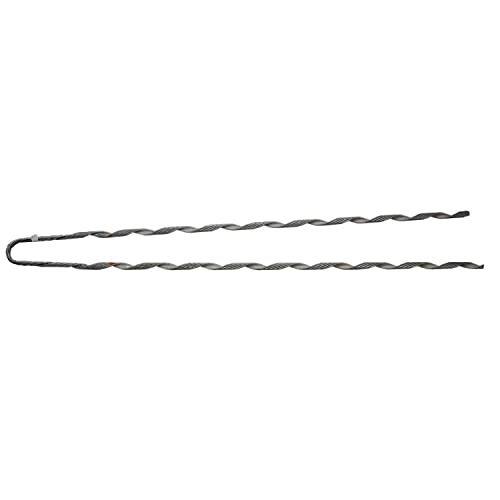
A big grip dead end is a component used to secure and terminate the ends of conductors in the transmission system. It plays an important role in the structural integrity and performance of the lines. This helps to ensure the safe and efficient delivery of electricity. It has designs to grip the conductor and prevent it from slipping or being loose. It also serves as a means to terminate the conductor to provide a stable endpoint for the line. The big grip dead end is from materials designed to withstand harsh environmental conditions. These materials include steel, aluminum or galvanized steel. Using big grip dead ends provides several benefits to transmission and telecommunication networks. These include conductor damage prevention, support, mechanical strength and durability.
Differences between dead end cable grip and big grip dead end
These are both components used in transmission lines but they have different purposes. They have different characteristics, functions and work in different locations along the line. Dead end cable grips provide support along the length of the conductor. The big grip dead end terminates the conductor at the end points. The following are the notable differences between the two components.
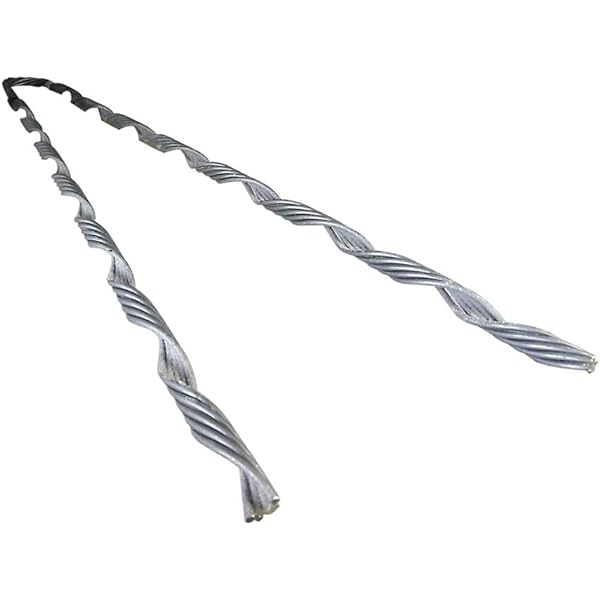
- Functionality – dead end cable grips have designs to provide grip and support along the length of the conductor. They distribute the tension and prevents conductors from sagging or vibrating. Big grip dead ends have designs to terminate the end of the conductor. They provide a secure attachment point and anchoring to conductors.
- Location of use – dead end cable grips install along the length of the conductor at transitional points. Big grip dead ends install at the endpoints of the transmission line.
- Design and construction – dead end cable grips are flexible and can hold variations in conductor diameter. They are from materials like steel or synthetic fibers. Big grip dead ends are more rigid and strong to provide a secure termination point for the conductor. They can have a clamp or grip mechanism that attaches to the conductor.
- Load capacity – dead end cable grips have designs to handle the tension and load applied along the length of the conductor. Big grip dead ends have designs to withstand the greatest tension and load at the endpoints.
Challenges and issues facing use a big grip dead end
There are several challenges and issues facing use of big grip dead ends. The challenges need research to address them. It also requires collaboration among manufacturers, utility companies and regulatory bodies to address the challenges. They can lead to the development of best practices for the design, installation and maintenance. The following are the challenges and issues facing use of big grip dead ends.
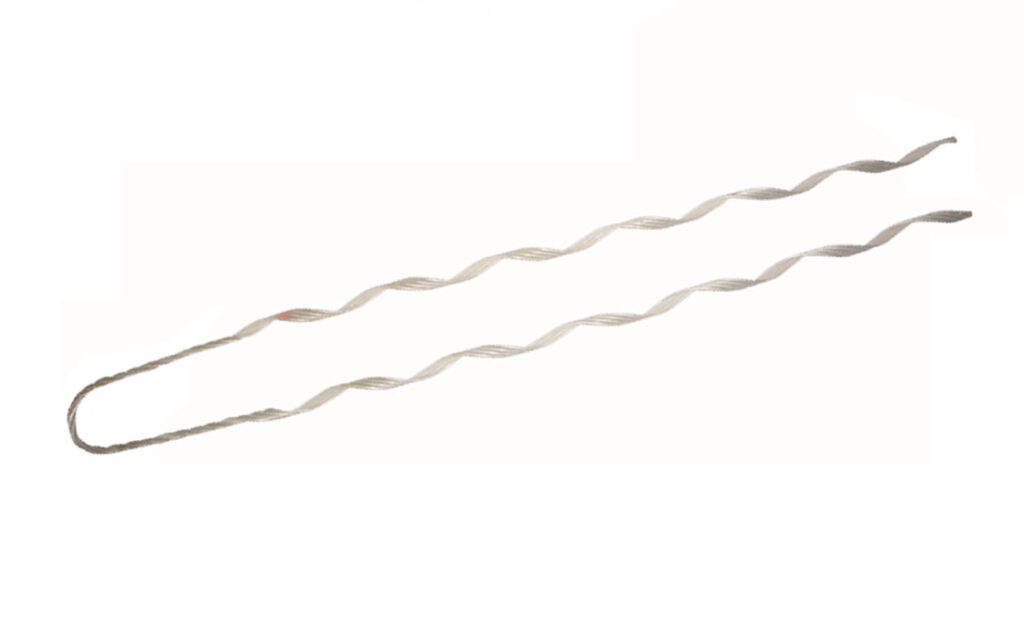
- Installation complexity – proper installation of the dead ends needs specialized knowledge and equipment. Ensuring the correct tensioning of the conductor and proper attachment of the dead end can also be challenge.
- Corrosion and degradation – big grip dead ends face corrosive elements like moisture, salt and chemicals. Presence of corrosion leads to the weakening of the structural integrity of the dead end.
- Environmental impact – manufacturing of big grip dead ends can have implications. This is including energy consumption and emissions. Improper disposal of damaged dead ends contributes to pollution and resource depletion.
- Maintenance requirements – big grip dead ends may experience wear and tear due to exposure to environmental factors. These factors include UV radiation, temperature fluctuations and mechanical stress.
- Compatibility and standardization – compatibility issues may arise while using big grip dead ends with conductors of different sizes. Standardization of components can help mitigate these issues.
- Safety concerns – working on high voltage transmission lines poses different safety risks for workers. Proper training, adherence to safety protocols can help to mitigate these risks.
Surface coating and treatments for big grip dead ends
Big grip dead ends may contain surface coatings or treatments to enhance their performance and durability. Choice of the surface treatments depends on factors like operating environment, expected lifespan and aesthetic requirements. Also, the proper surface preparation and application ensures the effectiveness and resistance to environmental factors. The following are the common surface coatings and treatments for big grip dead ends.

- Galvanization – this involves applying a layer of zinc to the surface of the big grip dead end. This coating protects the dead-end rom rust and oxidation in harsh environments.
- Powder coating – this involves applying a dry powder to the surface of the big grip dead end. It is then cured under heat to form a durable protective layer. They offer resistance to impact, chemical and UV radiation.
- Painting – this is a simple surface treatment for dead ends in outdoor applications. They provide protection against corrosion, UV damage and environmental exposure.
- Chromate conversion coating – these are chemical coatings applied to aluminum dead ends. They help to improve corrosion resistance and enhance paint adhesion.
- Anodization – this is an electrochemical process that creates a protective oxide layer on the surface of the aluminum big grip dead ends. The layer improves corrosion resistance and enhances appearance of the dead end.
- Epoxy coating – this works as a protective layer over the surface of the big grip dead end. The coatings offer resistance to chemicals, abrasion and corrosion.
- Passivation – this is a chemical treatment process used to remove free iron from the surface of stainless steel. It provides an oxide layer that improves corrosion resistance and helps maintain the integrity of the stainless-steel surface.
Cost considerations and comparisons for big grip dead ends
Big grip dead ends come in different prices from different suppliers. It is important to compare different types or brands of dead ends for better decision making. Additionally, it is advisable to consider upfront costs, maintenance, repair and replacement costs. Price ranges of big grip dead ends vary depending on working load limit and size. These prices range between $20 -$100 + for small to large dead ends. the following are the factors affecting the prices for big grip dead end.
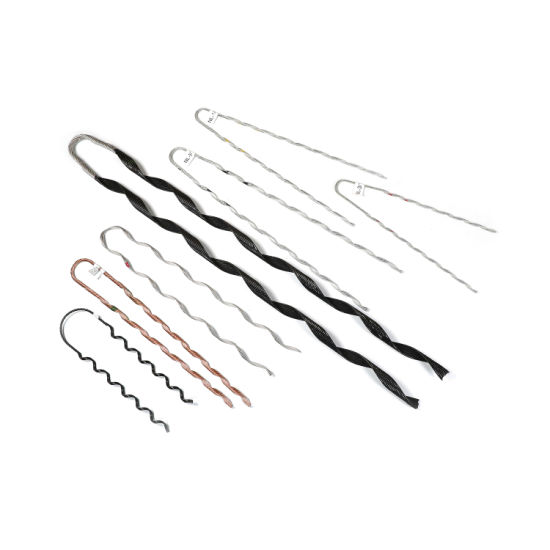
- Material cost – the main material used for the big grip dead end influences the prices. The cost of these materials varies depending on factors like market prices, quality and quantity purchased.
- Quality and durability – higher quality materials and construction methods result in durable and reliable grips. They may also have a higher upfront cost but may provide cost savings. This is by reducing maintenance and replacement costs.
- Supplier and brand – availability of different suppliers and brands may offer big grip dead ends at varying prices. This is depending on reputation, market demand and value-added services.
- Manufacturing process – the process involves machining, welding, coating and assembly. The design complexity and efficiency of the production process impacts the manufacturing costs.
- Installation costs – the installation needs skilled labor and specialized equipment. Factors like accessibility, terrain and weather conditions can influence installation costs.
- Project scale and volume – purchasing in bulk may allow for economies of scale projects which may incur higher costs.
- Regulatory compliance – compliance with industry standards and regulations may add extra costs to the manufacturing and testing processes. Compliance with standards can help avoid potential liabilities and ensure the safety and reliability of the systems.
Selecting the right supplier or vendor for dead ends
There are several factors to consider when selecting the supplier for big grip dead ends. This includes factors such as product specifications, availability, lead times and pricing. Also, it is advisable to request for samples to check the quality and suitability of the products. The following are the factors to consider when selecting supplier or vendor for big grip dead ends.
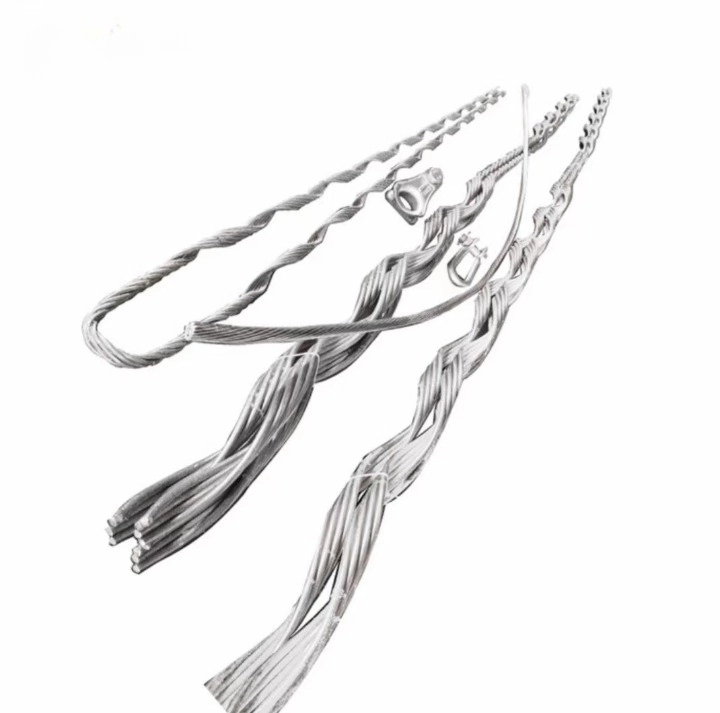
- Product quality and reliability – select suppliers that provide high-quality big grip dead ends that meet industry standards. Consider material durability, corrosion resistance and load bearing capacity.
- Customization and flexibility – the supplier should accommodate specific project requirements. This is including custom designs, sizes or coatings that fit your needs and specifications.
- Cost and pricing – as for quotes from different suppliers to ensure you get competitive rates for the dead ends. consider product quality, reliability and extra services offered.
- Recommendations – look for references or recommendations from industry experts or colleagues. Select the supplier that can provide insights into their reliability, performance and customer satisfaction.
- Industry experience and reputation – select suppliers with a proven track record of producing big grip dead ends. Check their customer reviews, testimonials and case studies.
- Lead times and availability – heck the suppliers lead times and production capabilities to ensure timely delivery. Consider manufacturing capacity, inventory levels and order fulfilment.
Frequently asked questions
Big grip dead ends are components used to securely terminate the ends of conductors. Their purpose is to provide a stable attachment point for the conductor at the endpoint of the transmission line.
Challenges with big grip dead ends include installation complexity, maintenance needs, corrosion and degradation.
Surface coatings and treatments include galvanization, epoxy coating, powder coating, anodization, passivation and chromate conversion coating.