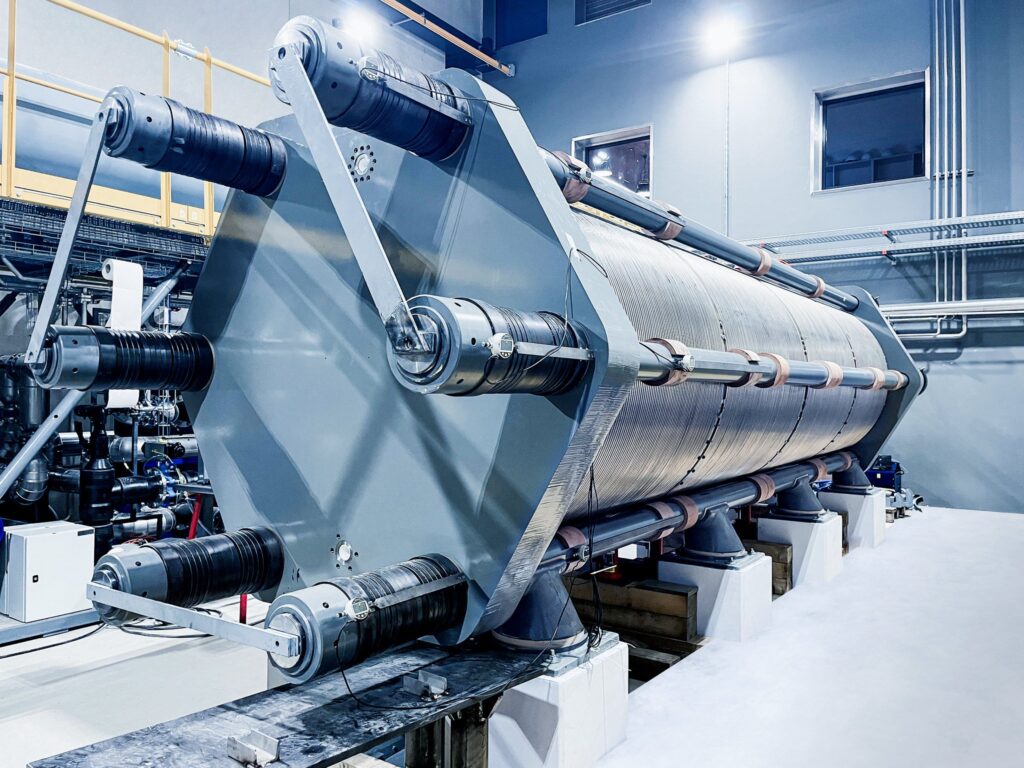
Chile is emerging as a global green hydrogen industry, thanks to its rich solar and wind resources. Electrolyzers play an important part in the production of green hydrogen for the energy transition. Electrolyzers convert water into hydrogen and oxygen using renewable energy. Corfo has awarded Chile $25.6 million in financing, allowing it to establish its first electrolyzer facilities. Corfo’s initiative will allow for the installation of plants in Chile with a total investment of more than $50 million. Green hydrogen is critical to Chile’s renewable energy economy. It replaces coal, natural gas, and diesel in mining operations. Electrolyzers use steady and high-quality electrical current to divide water via electrolysis. High-quality conductor splices maintains the integrity of electrical connections, reduces resistance, and ensures optimal performance of the electrolyzer stack.
A well-designed conductor splice minimizes energy loss during transmission. This is critical for the effectiveness of renewable energy consumption in electrolysis. Chile is increasing its green hydrogen production. This requires the reliability of electrolyzer components. High-quality conductor splices cut downtime and maintenance expenses. It enables large-scale deployment of electrolyzers. Conductor splices must be long-lasting and resistant to external variables such as temperature variations, dust, and humidity. This is critical because Chile wants to manufacture some of the cheapest green hydrogen to stay competitive in international markets. Conductor splices are critical in connecting electrolyzers to renewable energy sources.
Key projects and their impact on Chile’s renewable energy industry
Chile is strengthening its green hydrogen sector by launching three major electrolyzer projects. The efforts are likely to have a variety of impacts on Chile’s energy landscape. Key projects include AES Chile’s Inna, a large-scale renewable hydrogen and ammonia manufacturing facility. These projects seek to maximize the region’s renewable energy potential. Engie & Walmart Chile’s green hydrogen facility demonstrates the practical use of green hydrogen in logistics and supply chain activities. These initiatives have an impact on Chile’s energy industry by diversifying energy sources, promoting decarbonization, and driving economic growth.
The function of conductor splices in electrolyzer factories
Conductor splices provide efficient and dependable electrical connections in electrolyzer facilities. Electrolyzers use high-voltage, high-current electricity to convert water into hydrogen and oxygen. Conductor splices aid to maintain electrical continuity, lower resistance, and improve system reliability. High-quality conductor splices cut downtime, increase efficiency, and improve safety. Compression splices, mechanical splices, heat-shrink and cold-shrink splices are among the most common electrolyzers used in electrolyzer factories. Their main roles include:
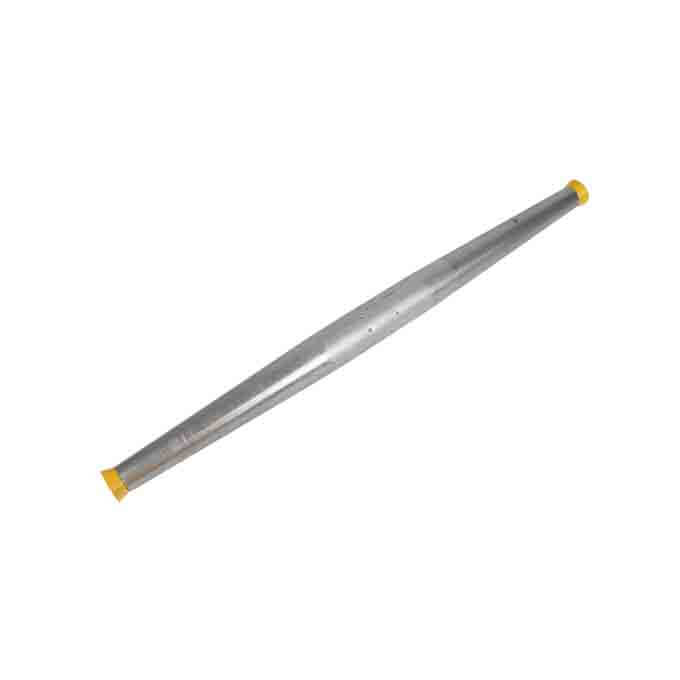
- Ensuring efficient power transmission—electrolyzers need consistent and high-power electrical input from renewable energy sources. Conductor splices help connect and extend power cables to ensure seamless electricity transmission.
- Reducing electrical resistance and energy loss—poor electrical connections can lead to voltage drops and overheating. High-quality conductor splices reduce resistance at connection points to ensure optimal energy flow.
- Enhancing system reliability—Electrolyzer factories operate in areas where vibration, temperature changes, and corrosion can affect electrical connections. Conductor splices provide durable, secure connections that prevent power failures and electrical hazards.
- Supporting modular electrolyzer designs—large electrolyzer plants have modular designs that need flexible expansion. The use of conductor splices allows new electrolyzers to integrate easily into these designs.
Technologies that support the growth of Chile’s electrolyzer industries.
There are significant improvements that will ease the construction of electrolyzer facilities in Chile. Electrolyzer technology is projected to begin operations in 2026, supporting breakthroughs in energy, automation, and infrastructure. The success of electrolyzer factories will be determined by these technologies. They can improve efficiency, scalability, and cost effectiveness. These are the essential technologies.
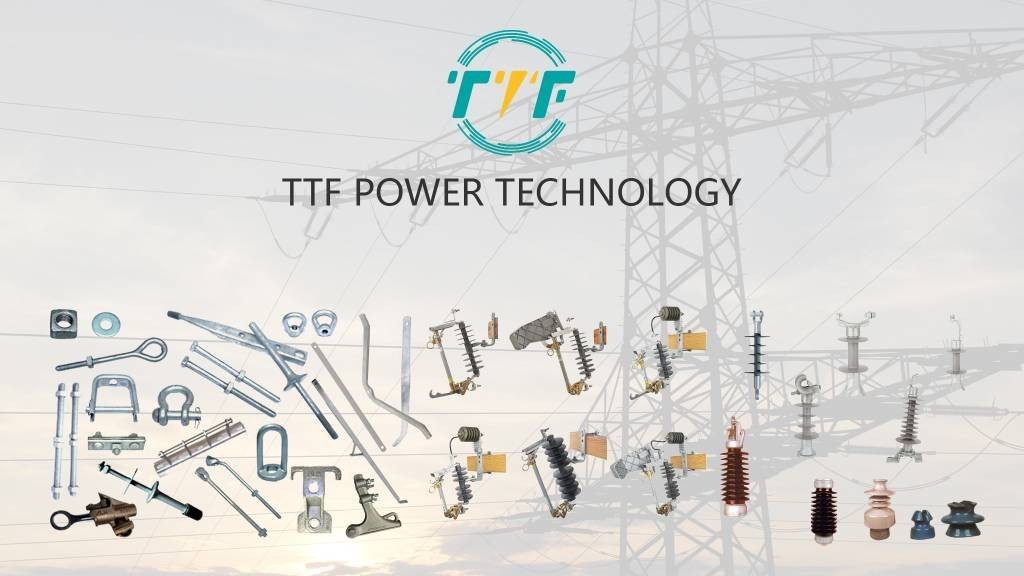
- Advanced electrolyzer technologies—these include proton exchange membrane, alkaline electrolyzers, and solid oxide electrolyzers.
- Renewable energy integration—this includes smart grid and AI-driven energy management and hybrid solar-wind energy systems. Conductor splices help n integrating these technologies into electrolyzer factories.
- Digital and automation tech—industrial IoT and predictive maintenance reduces downtime, extends equipment durability, and improves operational efficiency. Also, robotics increase production speed, reduce costs, and enhance quality control in electrolyzer factories.
- Hydrogen storage and distribution innovations—advances in hydrogen storage allow for safe and efficient long-distance transportation. Also, green hydrogen can be converted into ammonia and e-fuels to make it easier to store and transport.